Mon October 30, 2023
Wirtgen Group
For screening high-quality silica sand in a sand pit in the administrative district of Sigmaringen (Germany), trust was placed in the mobile screening plant MOBISCREEN MSC 702i EVO with Dual Power.
The processed material is then used, among other things, for sports ground construction and in glass production or for building material such as plaster or adhesive.
Effective Solution, Climate-Friendly Operation
After a search for an efficient solution for separating the grain sizes, the operating company decided on the MOBISCREEN MSC 702i EVO with Dual Power.
On the one hand, the screening plant has a wide, large screening surface that can deliver a very high output. On the other hand, Kleemann provides an option for all-electric operation of the plant — a future-oriented drive system that works on site without CO2 emissions: A positive feature for the environmental balance and quality assurance.
To guarantee the power supply on site, the company built a transformer station that accompanies the machine, which is moved 2–3 times a year.
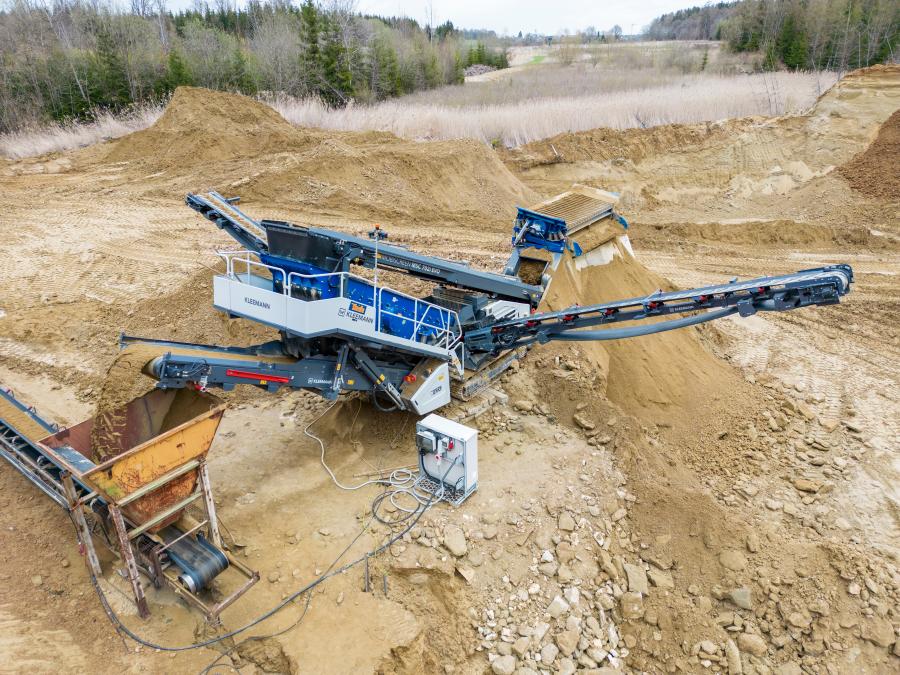
The MOBISCREEN MSC 702i EVO is operated in a silica sand pit in Meßkirch-Rengetsweiler (administrative district of Sigmaringen) purely by electric power.
Demonstration of New Acquisition Impresses
The new acquisition is the first plant in the operating company with an electric drive. Achim Haßdenteufel, section manager at Emil Steidle GmbH & Co. KG, and his team were already thrilled with the plant performance during the first test run.
"We looked at different plants, tested them on site and compared the output. Our material here is very specific. We have a lot of clay in the raw sand that clogs the screens," said Haßdenteufel.
And Facility Manager Walter Kieper added, "The machine has an impressive output. Everything can be operated very conveniently by remote control. Although our employees, who have been used to control via hydraulic levers up to now, had to reorientate, they quickly managed to cope with the digital display. Everything is clearly arranged and it has an intuitive design."
Details Make the Difference
The refined technical details of the MSC 702i EVO meet the high demands of the material. The configuration of the belts on the plant, for example, can be mirrored. The fine grain conveyor and middle grain conveyor can be installed either on the right or left and the travel distance of the wheel loader can be kept as short as possible. This also reduces the power consumption and wear on the vehicles.
The MOBISCREEN MSC 702i EVO is equipped with a vibrating slotted grate. Large sand stones can thus be separated in advance and the machine can be loaded with a 0 - 50 mm feed size. The upper deck is used as a relief deck; the second deck defines the target grain size.
The stepless setting option of the belt speed contributes to energy efficiency: As the screening process in the sand pit merges the discharge of the middle grain conveyor and fine grain conveyor, only one side discharge conveyor is actively operated. The speed of the second belt is throttled to save energy. The reduced speed also is an advantage when the feed material is very wet, as Michell Blasczyk from WIRTGEN DEUTSCHLAND Vertriebs- und Service GmbH explained.
"Sand is not always the same. Depending on moisture content and properties, the covering, inclination angle, speed and many other factors must match exactly," said Blasczyk.
During setup, the operating company also placed its trust in support from the Kleemann experts — among other things, from specialist departments who prepared precise flow charts or the Kleemann laboratory that examined the material exactly in advance.
For more information, visit www.wirtgen-group.com.
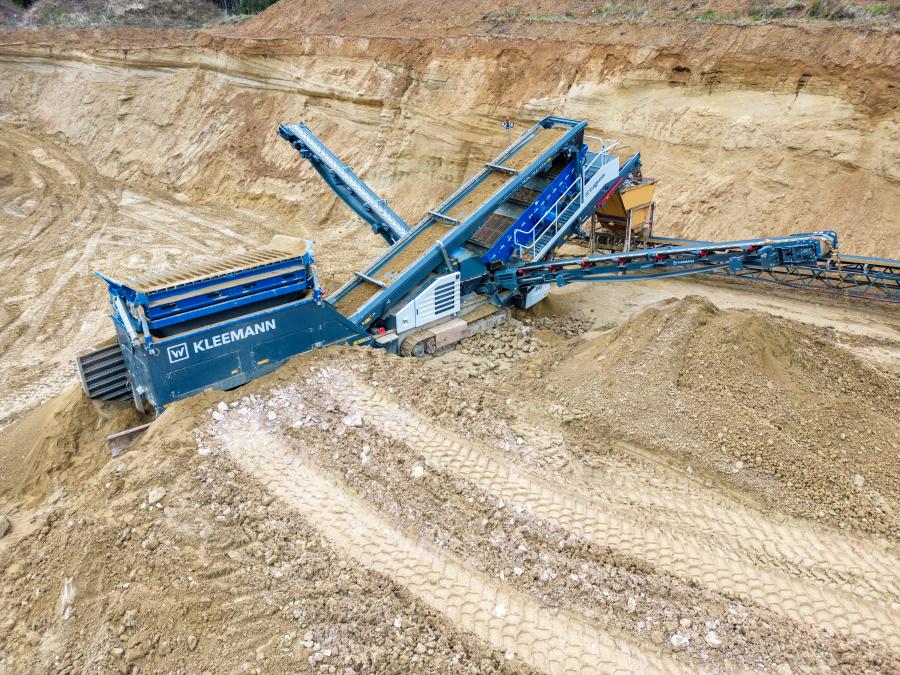
The classifying screen from Kleemann is equipped with a vibrating slotted grate. Large sand stones are thus separated in advance